The Minimak & Tokamak Outdoor Ovens
We are currently in development of our prototypes.
The Minimak and Tokamak progress is shown below, both builds are out of the concept stage and have moved to the first prototype. Both the Minimak and Tokamak are well on their way.
We have recently completed the first tests on our small pizza oven, the Minimak, and were pleasantly surprised with the results. We can cook a 12″ (30cm) pizza within 90 seconds. We cooked six pizzas.
Naturally as the unit cools, the cooking time extends. (Without additional fuel being added.) The last test pizza required 3 minutes. It appears we could have pushed the pizzas deeper and loaded more than one at a time, there is certainly enough room for two, if not four pizzas. (If the coals were to be pushed further away.) Images Below.
Although the inner chamber was intended for cooking or smoking, we had requests to investigate the oven’s ability to make Biochar. During warmup we used the inner oven chamber to make some biochar for the garden. We wanted to test this option to see if it was plausible. The biochar results are posted below.
Notably, we were very pleased with how clean the stack was. Besides the initial ignition smoke, the Minimak produces almost no smoke at the chimney, meaning it has a very low particulate emission and therefore much better for the environment. Furthermore, during the biochar making process the inner oven is in pyrolysis mode, meaning that it is mainly using the gasses coming off the wood as fuel leaving behind most of the carbon. A form of carbon sequestering carbon if you like. Interestingly, we’ve discovered that this chamber holds a significant amount of heat for a long time. After the biochar was made and later removed, it significantly assisted with the efficient pizza making . This excess heat could be used to cook other delicious food or perhaps some other useful application. The unit had reached 1112°F (605 °C) peek temperature during pyrolysis. At the end of the pizza making process the inner oven was still at 698°F (370°C).
During the trials, we discovered that the specialized industrial fan had failed. We were able to replace it with some domestic fans we had on hand, which turned out to be more than sufficient to provide the required air for an efficient and clean burn. This has certainly reduced the cost of the unit and makes it far easier to maintain by a potential owner.
There was a necessary redesign of the doors on the Minimak. It was not sealing properly and creating poor convection flow, unwanted smoke and some small combustion outside the oven. Images Below
We were able to modify the door locking mechanism which resolved these issues. The new system now pulls the door tighter into place, compressing the seal tightly. During the second run, with the new door, we managed to cut the warmup time from 60 minutes down to 30 minutes. We should also note that the biochar making process only takes 30 minutes using maximum wood cross section of 1″ (25mm). Additional biochar batches, take only 30 minutes, since the oven had good heat retention.
The third run we got the Minimak quickly up to temperature and after making some biochar we made 16 pizzas. Starting from 90 second cooking time and ending with a 4 minute cooking time.
So what’s next?
These trial runs have given us a list of improvements and they are as follows:
- Change airflow pipes for cleaner combustion.
- Put door improvements into the production version.
- Add misting lance for dealing with biochar.
- Decouple unit from the resting surface.
- Offset lifting lugs for easier lifting for transport.
- Install Additional access points for extracting wood vinegar.
- Install thermocouples for temperature monitoring.
- Decouple side covers from main body.
- Install thermal shields at each end of unit.
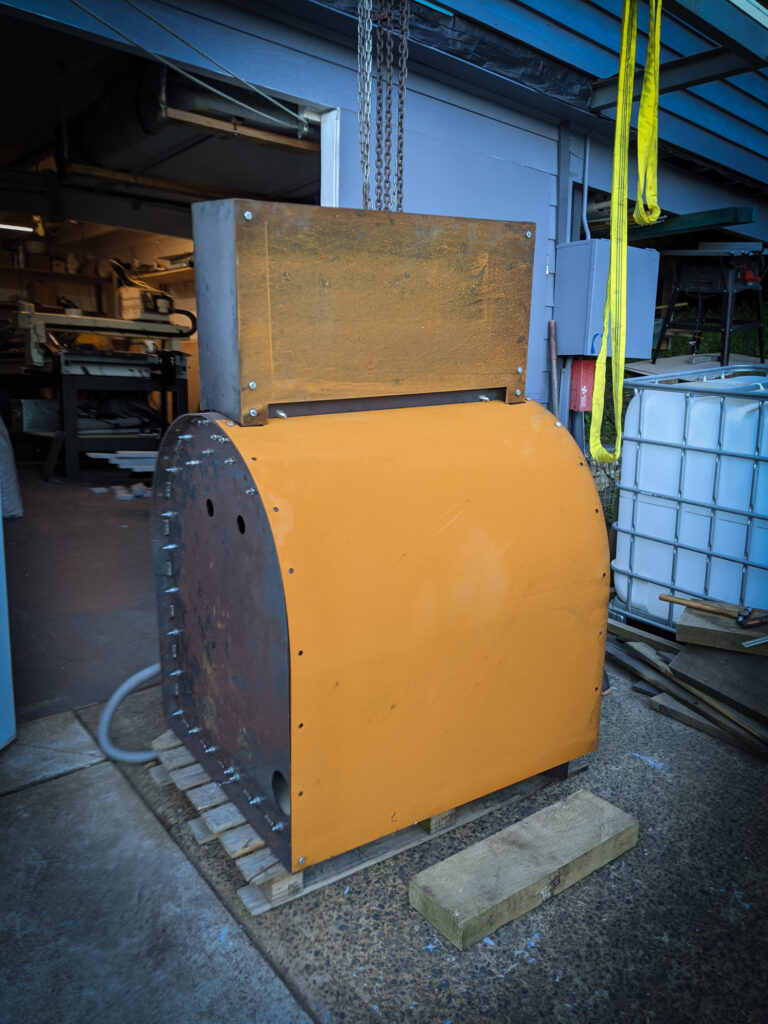
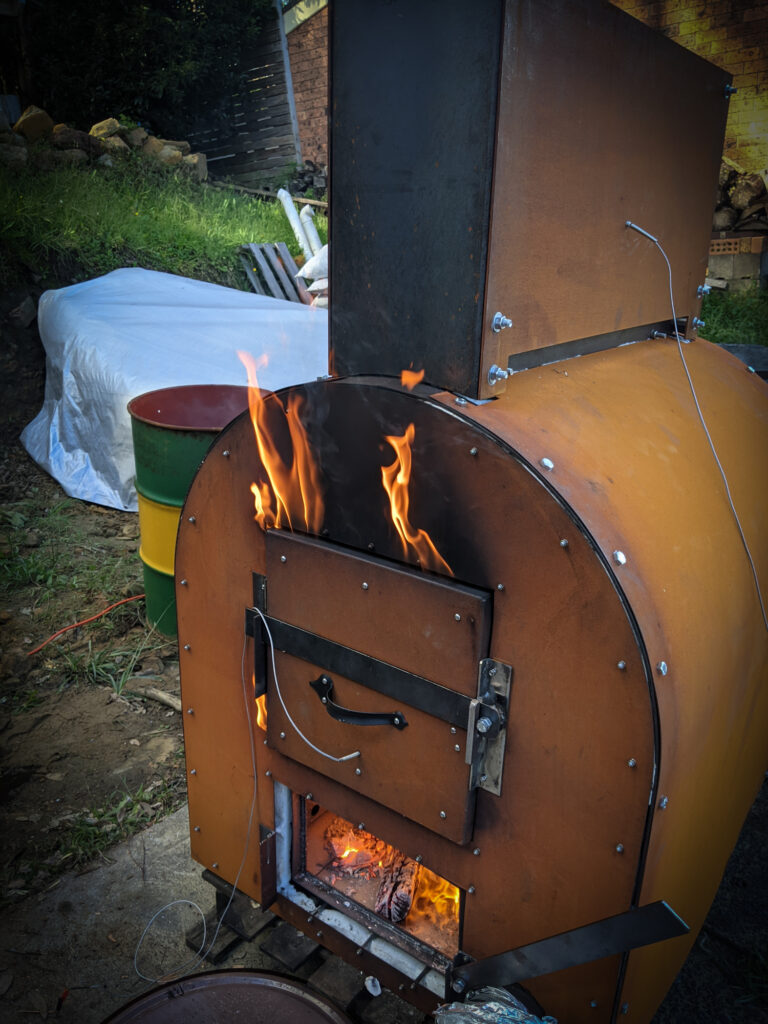


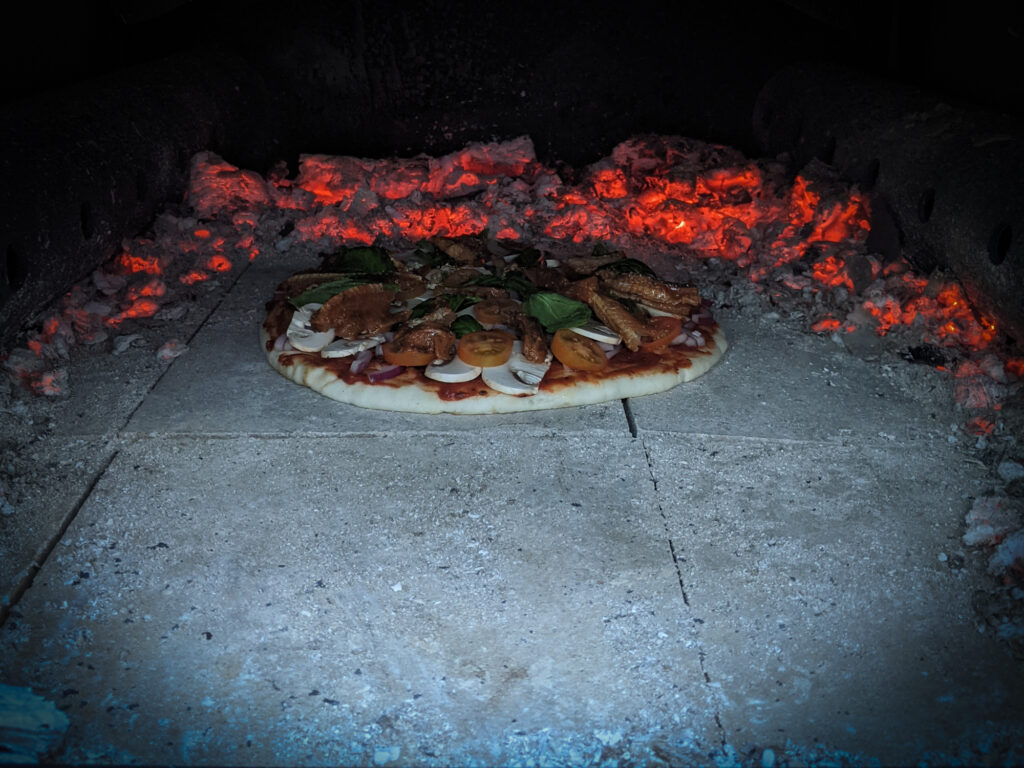

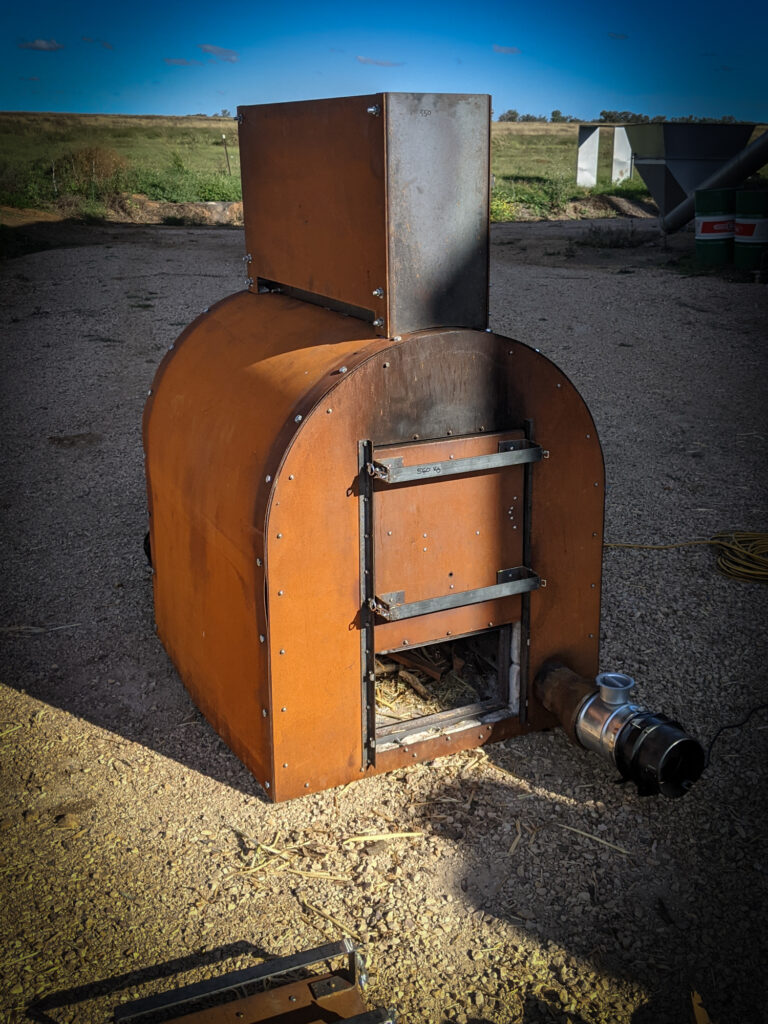
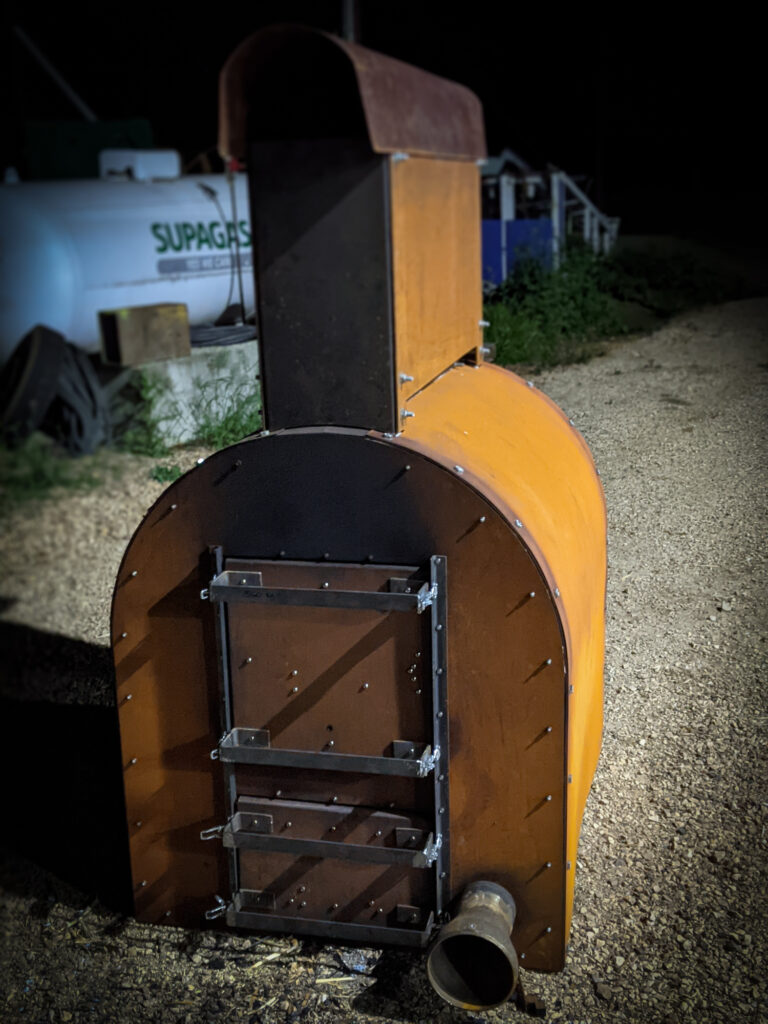
Minimak SEM Analysis Results
We have recently tested the first batch of biochar from the Minimak trials. The results show the incredible microstructures of the biochar, these micro-pores are fantastic for water retention, storage of beneficial elements for plant growth, as well as providing surfaced that encourage the growth of beneficial microorganisms and bacteria.
The test was performed by Professor Stephen Joseph using the Phenom-World Scanning Electron Microscope. Besides SEM imagery the unit can provide chemical analysis as well. Below, you can see the SEM images as well as a table of the chemical composition inside the biochar which was made during the first run of the Minimak. As you can see there are good amounts of available elements for plants to access, making this a fantastic slow release fertilizer.
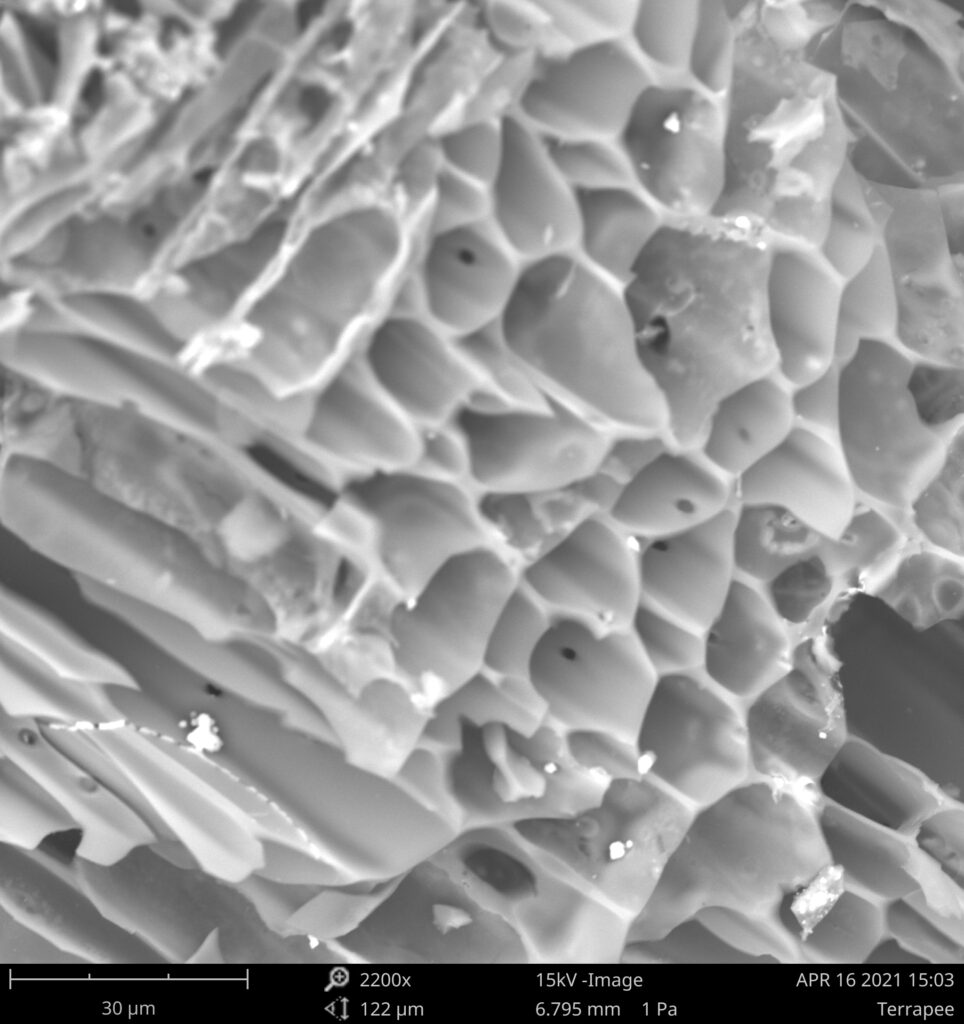
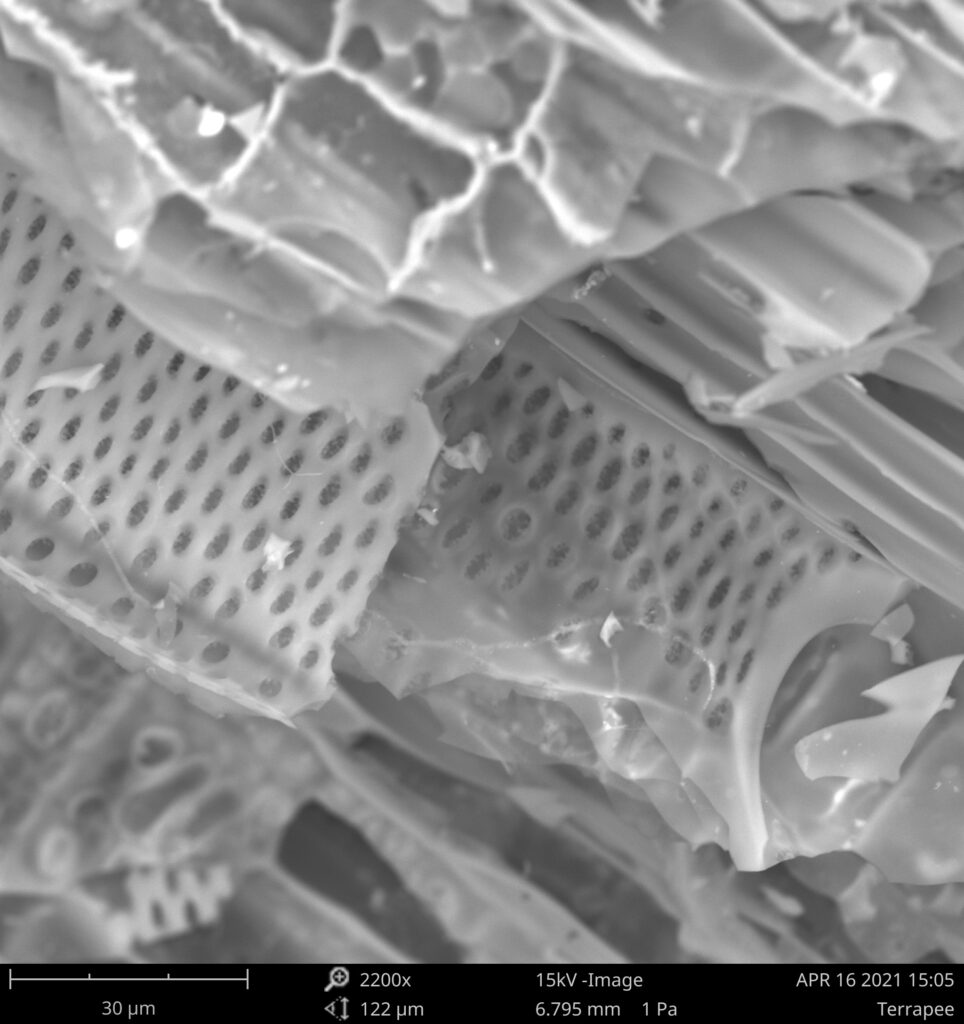
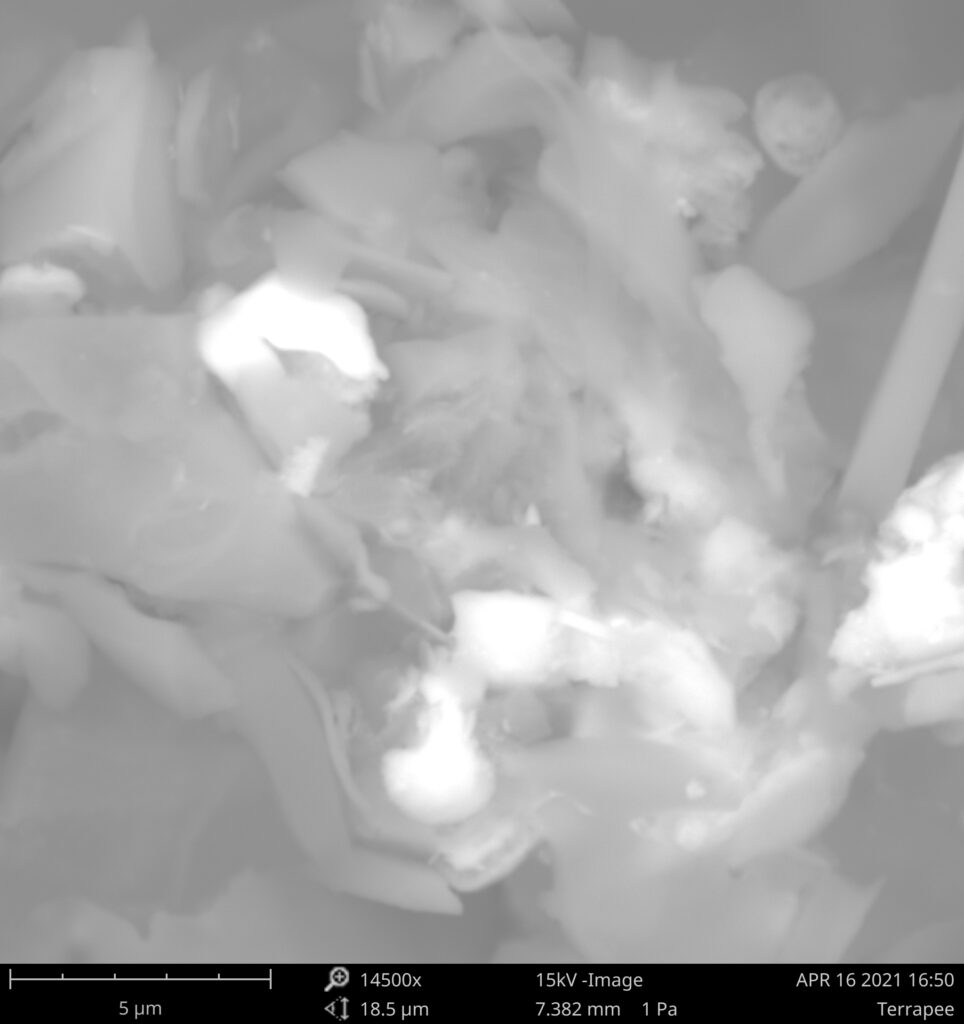
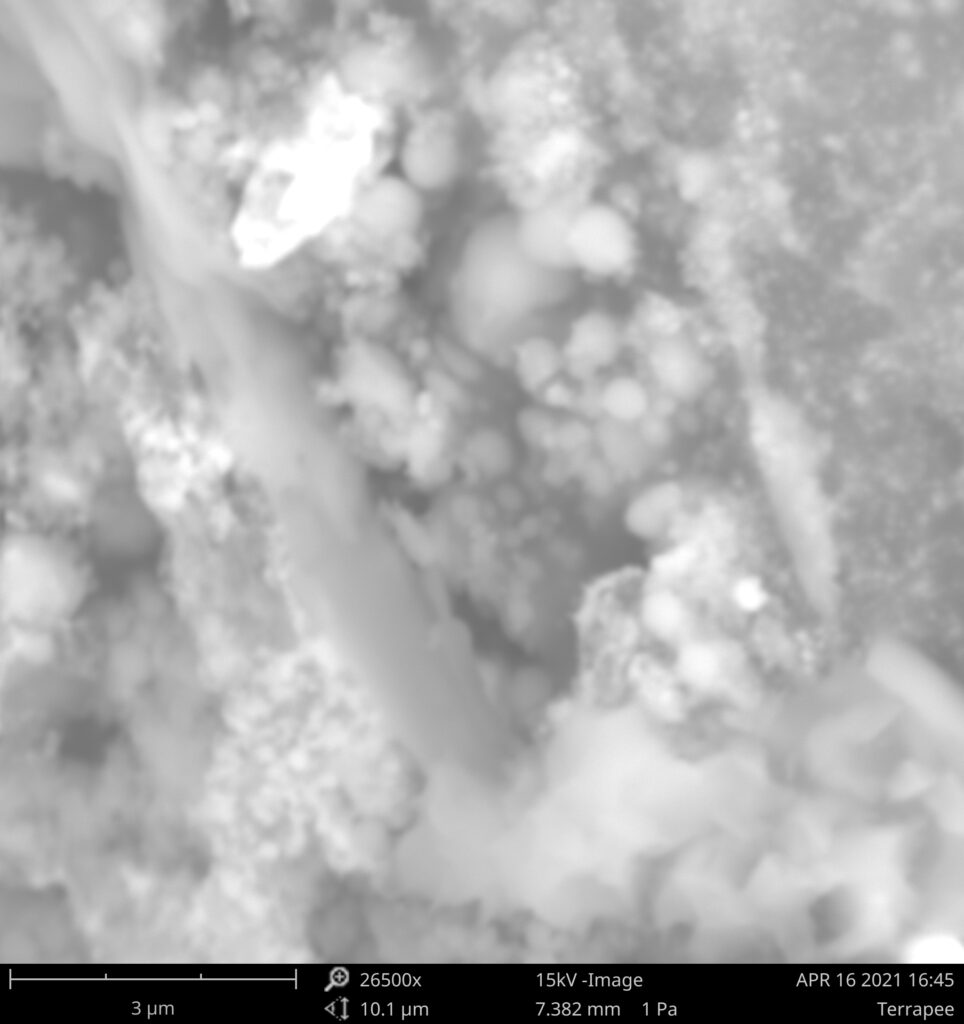

Element Symbol | Atomic Concentration | Weight Concentration |
---|---|---|
O | 58.32 | 47.74 |
C | 17.01 | 10.45 |
Na | 5.73 | 6.74 |
K | 5.27 | 10.55 |
P | 3.45 | 5.46 |
Fe | 3.13 | 8.93 |
Si | 2.66 | 3.82 |
N | 1.37 | 0.98 |
Ca | 1.27 | 2.61 |
Cl | 0.62 | 0.62 |
Mg | 0.62 | 0.77 |
Al | 0.30 | 0.41 |
S | 0.24 | 0.40 |
The Tokamak Outdoor Oven
Although the Tokamak was the first off the prototype line, we manufactured the unit in Australia, in fact we had lots of help from Don Smith from Auger Fabrication. Don also is building a large scale biochar plant. Their company is called Envirochar. Images Below
The Tokamak development was paused to allow the Minimak build to take priority. We found it was easier to manage the field test on the smaller unit. It also made sense to try out new ideas on the Minimak first to save on costs.
We have the Tokamak alpha unit 75% assembled. We are currently working on the new features such as several clean emission solutions as well as designing a new airflow mixing system. Images Below
The refractory material solutions to keep the exterior of the unit cool, as well as heat efficient have worked out very well in the Minimak, considering that the amount is twice that of the Minimak we expect to see even better results on the Tokamak. We are also taking the thermal decupling and applying it to the Tokamak.
The full scale model of the air supply is almost ready. We will be performing flow tests within a fortnight. Pending the success of the test we will move onto installing the system as well as additional air scrubbing features and quenching/activation systems for the unit. Hoping to have a fully working unit before the end of June.
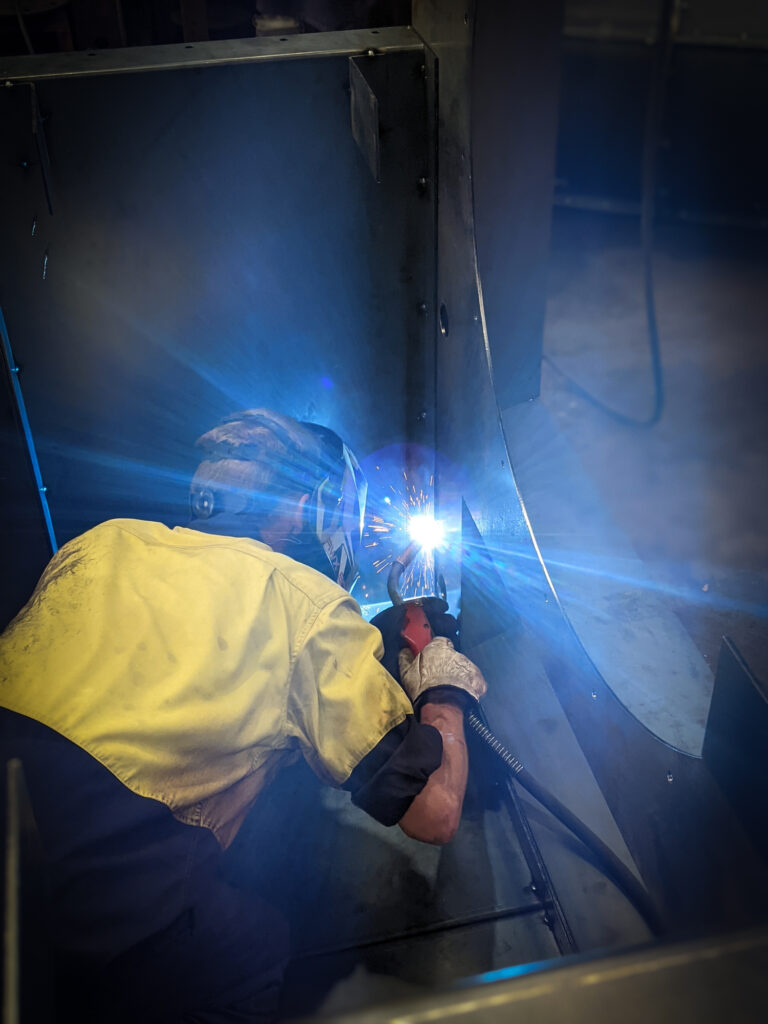
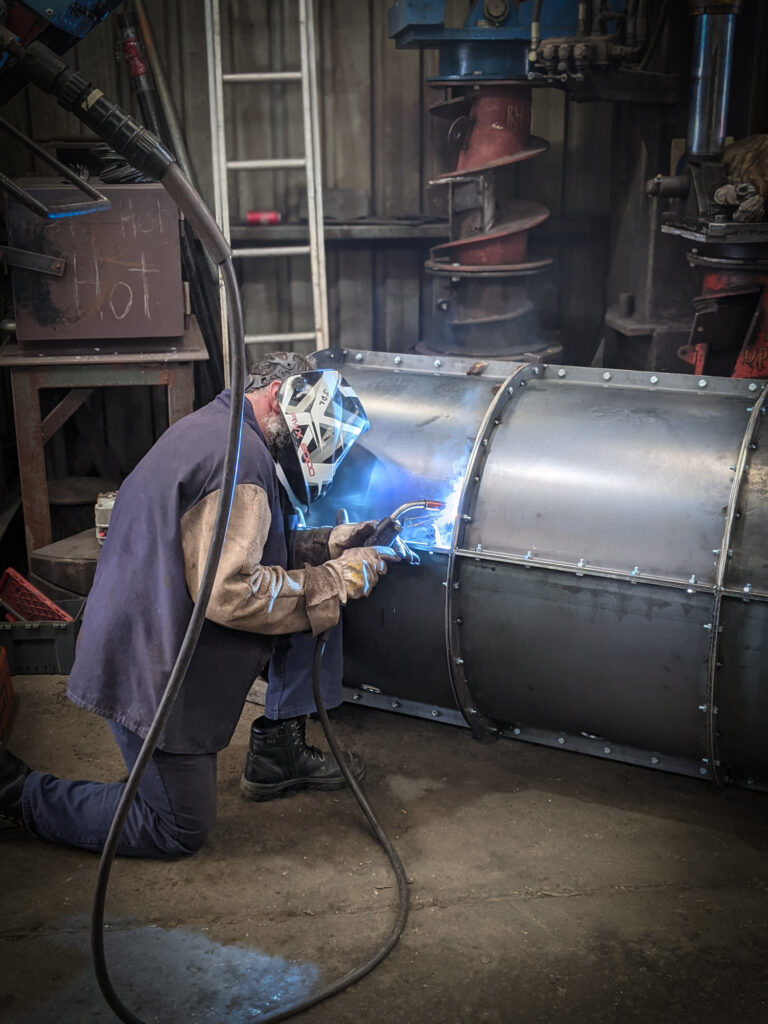
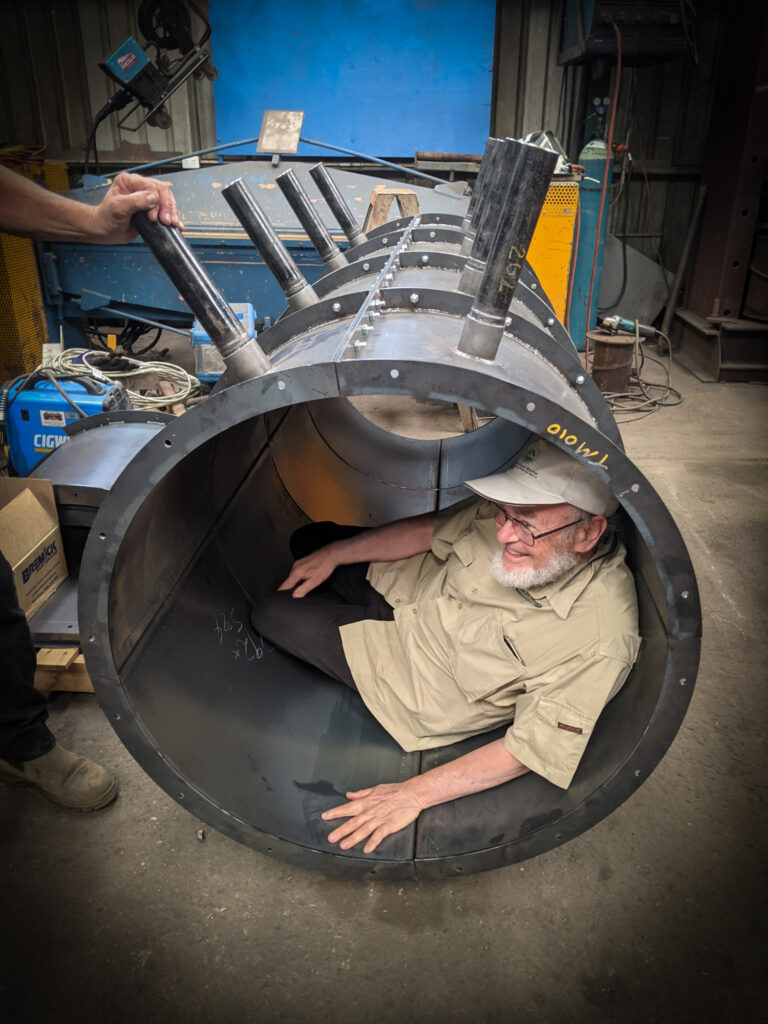
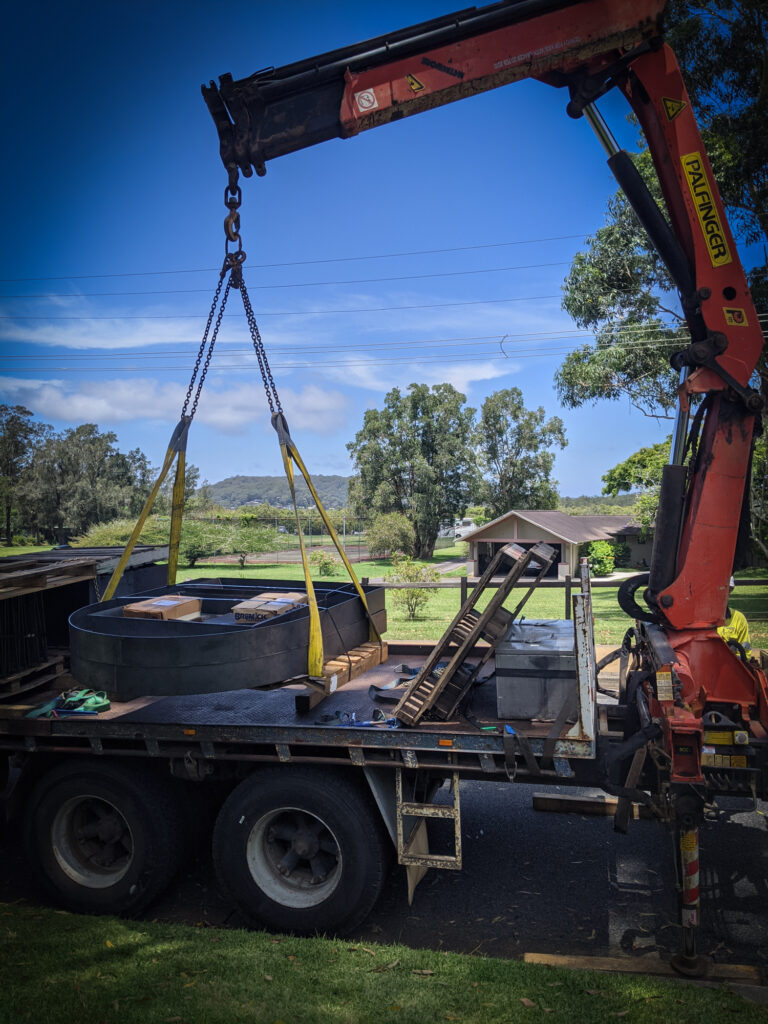
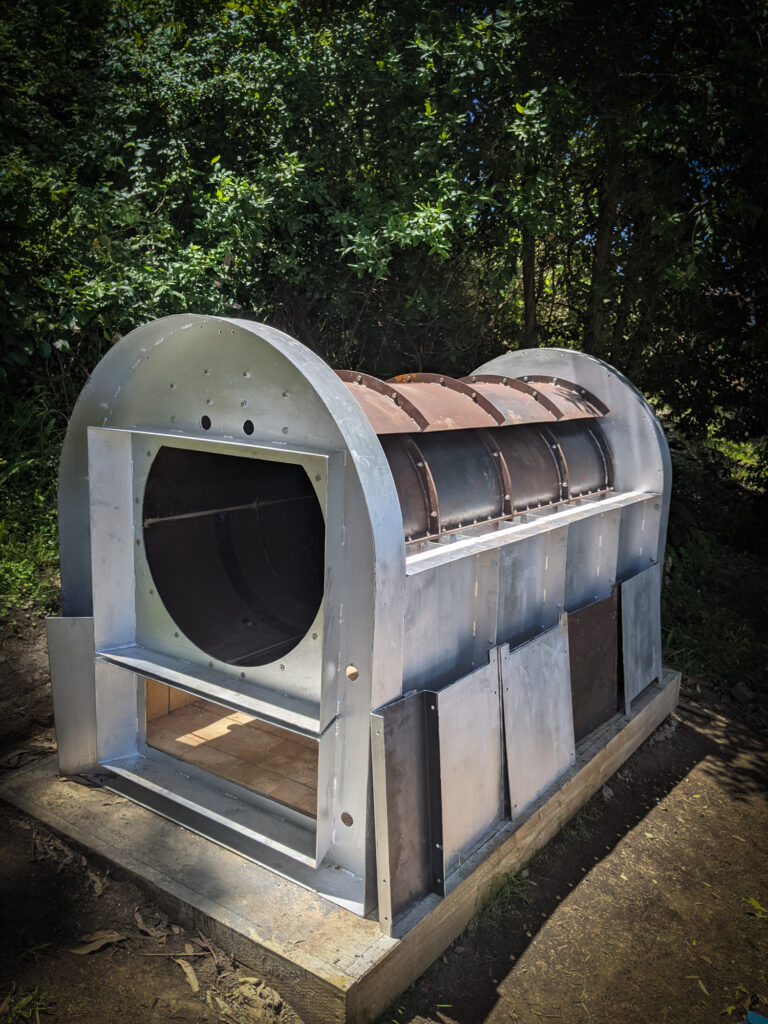
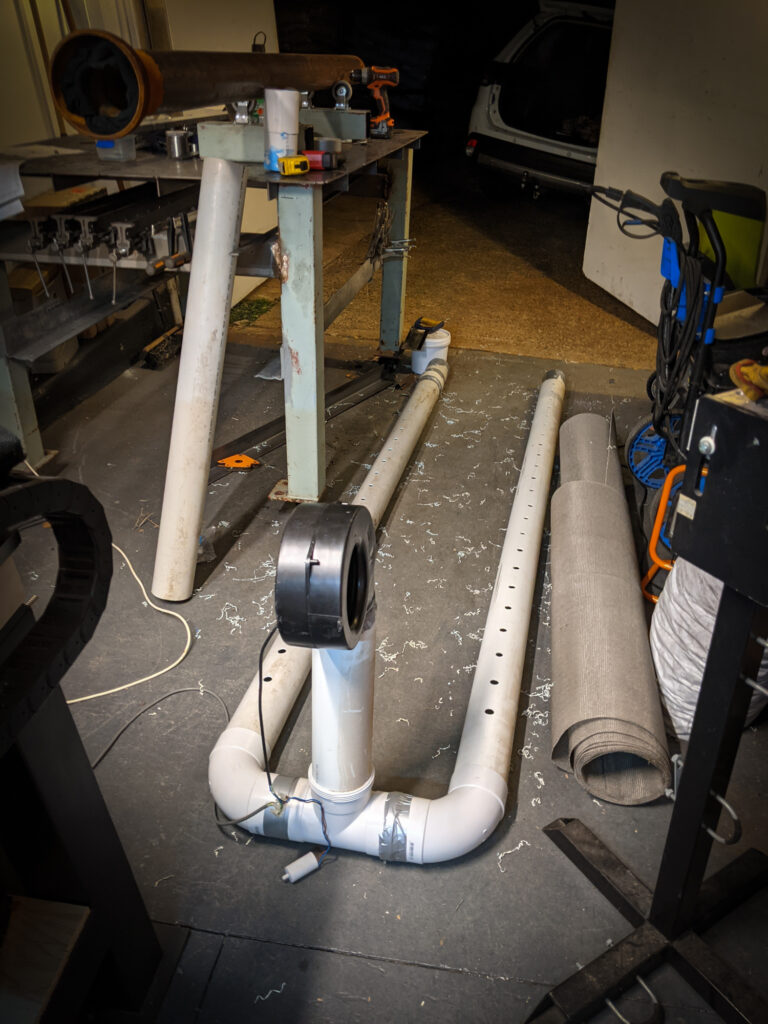